Select the open top type when moving the device in and out by auto loader, and the clamshell type when inserting and removing it by hand.
LGA socket
-
Burn-in Sockets
Reliability Assessment /
For Mass Production -
Test Sockets
Property Assessment /
For Mass Production
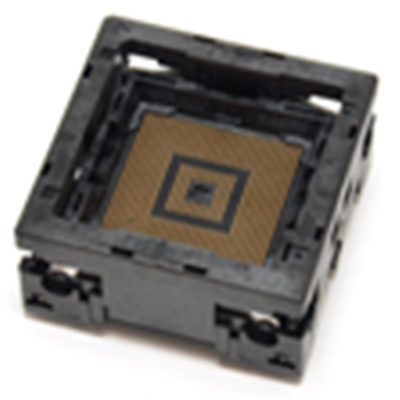
LGA Burn-in (BI) socket contacts the LGA pad to have an electrical connection. There are two kinds of contact. One is 2 point contact according to the pad size and pitch, and the other is conical 1 point contact. In addition, there are two kinds of socket frame. One is clamshell type, and the other is open top type that is available with a latch mechanism to prevent PKG pop-up. It is possible to attach a heat sink to the both socket types as a measure against heat generating PKG. Enplas Semiconductor Peripherals, the owner of this IC Socket Solutions.com, will solve all the problems of LGA BI sockets.
Key points for selecting a LGA BI socket Points
For LGA BI socket, it is necessary to select the optimum specifications depending on the usage, environment, and the function of device. Here are important points in determining the specifications of LGA BI socket.
Point#1
Select the method of setting the device from either open top or clamshell
Point#2
Select the implementing method on the board by either focusing on contact reliability or focusing on maintainability.
Select the implementing method on the board by either focusing on contact reliability or focusing on maintainability.
Precautions
Soldering method: Emphasis on contact reliability
There are two kinds of contact for this method, 2 point contactor with high contactability or 1 point conical contactor. These are available when terminal pitches are 0.65 mm or more with relatively large LGA pad. These sockets are relatively inexpensive because they are mainly made of molded components.
Surface mounting method: Emphasis on maintainability
The contact of this method is made by the bottom contact probe pin. Since the probe pin can move vertically, it can cover the warpage of PKG. With machining technology, it is possible to support multi-pitch and fine pitch of 0.5 mm or less.
Point#3
Consider methods for heat dissipation and large current depending on the characteristics of PKG
As a measure to prevent thermal runaway of heat generating PKG, apply a heat sink after performing thermal simulation. If it is for high currents, consider to use a bypass pin.
Common problems of Burn-in LGA socket Issues
Since LGA BI sockets need to keep stable performance even in harsh environments, it is necessary to incorporate measures to avoid troubles in advance by utilizing simulation technology. Here are common problems and solutions when using LGA BI sockets
Issues #1
Thermal runaway due to PKG's self-heating
Heat generating devices may cause thermal runaway in BI tests’ high temperature environments. If this happens, BI test cannot keep going.
Solutions
Utilize thermal analysis simulation and avoid thermal runaway by installing the optimum heat sink!
Issues #2
The Pad and pin do not make good connection
Even though sockets and devices are elaborately designed, if the PKG warps during the BI test, the position of Pads will change, which causes poor connection. If it is the case, BI test will not work, so it is necessary to ensure stable contact regardless of the PKG warpage.
Solutions
Select the most suitable one from 3 types of contact pin tip shapes!
Issues #3
Repeated BI testing worsen yield
For Au-plated contact pins, the base material of the contact pin may be exposed as the BI process is repeated. If this happens, the tin plating on the PKG Pad will be peeled off and transferred, and the contact between the socket (contact pin) and the device will become poor. As a result, the burn-in test will be NG and the yield will decrease.
Solutions
Achieve a long life with contact pins that use ES plating!
LGA socket
Solutions
-
Spring Probe Pin
Enplas's own design will provide internal short circuit of probe pin with low resistance value (Ave 50m ohm or under)
Enplas provides suitable socket design proposal to meet required specification -
Custom socket for high power liquid cooling system
Not only BGA, and LGA, but also various type of package including QFN can be designed by using a socket that is suitable for the thermal head size
-
LCF series (general-purpose molded frame)
Low price and quick delivery for various devices up to 100mmx100mm
Replacible on site by surface mounting method -
Carrier Socekt
Easy package handling with carrier PCB
Multi-height pusher for different thickness devices -
Sockets for power devices
Compatible with various power devices that are not handled by other companies
It is also possible to consider the optimum pin arrangement and support large currents of power devices. -
Improved cover handling socket for large devices
Enable to operate with stable pressing force for high pin count solutions.
-
Socket with heat sink
Heat Sink will reduce the increase of device temperature by contacting device surface with this parts and radiating the device heat into the air.
-
Burn-in socket with heat pipe
High heat dissipation performance due to the heat circulation structure of the heat pipe improves the accuracy of individual temperature adjustment tests for high heat generation PKG.
-
Individual Temparature Control System
Heater and temperature sensors can be attached to control the temperature of the device for each socket.
Achieves more accurate temperature control in comparison with general burn-in equipment (temperature setting ± 3 ° C) -
High pin count BGA socket (VC contact)
Stamped contact pin and molded frame realize significant cost reduction for large PKG
Replacible on site by surface mounting method -
ES Plating
By developing special plating (ES plating), the life of burn-in socket contacts has been extended in high temperature environments.
Maintenance costs have also been significantly reduced by reducing re-gold plating costs, etc. -
AM contact series
Low price and quick delivery for various devices by using machined Contact unit
Replacible on site by surface mounting method
Our lineup of LGA sockets for burn-in Lineup
Socket | Specification | Specification | ~100pin | 500pin | 1,000pin | 2,000pin | 3,000pin | 5,000pin | 7,500pin | 10,000pin |
---|---|---|---|---|---|---|---|---|---|---|
Clam Shell | C Socket (XXXL-LCF) | 0.6mm~1.27mm | PK SIZE □100mm | |||||||
C Socket (XXL-LCF) | 0.6mm~1.27mm | PKG SIZE □80mm | ||||||||
AM Socket (L-LCF etc) | 0.3mm~1.27mm | PKG SIZE □55mm | ||||||||
PS Socket | 0.15mm~0.65mm | PKG SIZE □55mm | ||||||||
Open Top | AM Socket | 0.3mm~1.27mm | PKG SIZE □33mm | |||||||
AM / PS Socket | 0.3mm~1.27mm | PKG SIZE □23mm |
Please feel free to contact us with
your questions regarding burn-in sockets.
Contact Us
- Is it possible to manufacture a socket with more than 10,000 pins?
- I am considering an electrical inspection methods for LGA ceramic packaging (20 to 50 mm) with several thousand pins. Do you have a suitable socket for this device?
- How do you prevent the BGA heating with the socket ?
- Can the BGA socket support ultra-fine pitch?
- What kind of analysis can you provide ?
- Is there export to overseas and get local support?
- What should I do if there is a problem?
- What is the guaranteed cycle?
- What temperature can it be used in?
- I would like to consider a burn-in socket, but what information do you need?
- How long does it take to deliver?
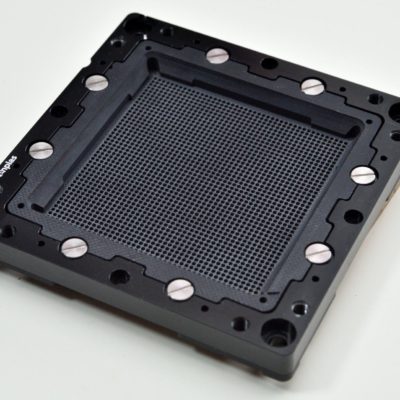
LGA Test sockets have electrical connection with PKG through contact pin and LGA pad. The contact pins used for LGA Test socket are probe pin (stamped probe) manufactured by Enplas’ original method and Capsule pin which gives stable measurement result regardless of high frequency. Because the contact pin holding part (contact unit) is removable, all contact pins are replacible by just replacing the units, or replacing a specific pin. In addition, the unit uses FR4 material, which has a cost advantage, and the target PKG size (pitch, number of pins, pin arrangement, etc.) can be changed by replacing the unit, so it can be used economically. It is possible to have it.
Key points for selecting a LGA Test socket POINTS
For LGA Test socket, it is necessary to select the optimum specifications depending on the usage, environment, and the function of device. Here are important points in determining the specifications of LGA Test socket.
Point1
Select the most suitable probe pin according to the requirements of electrical characteristics
If high frequency characteristics are important, select capsule content pin or coaxial contact pin
Point2
Select the pin tip shape and stroke amount for a stable contact
As for the crown shaped contact pin, the more protrusions the pin tip has, the more advantageous for contact stabiliby. Therefore, 4-point protrusion is applied, which is cost-efficient too. For even more stable contact, select conical 1-point contact. Also, select a pin stroke amount according to the testing machine.
Point3
Select the material of the contact pin tip depending on the required durability
In order to improve durability or to prevent Sn from adhering to the contact pin, there are some options for the contact pin tip, carbon coating, palladium alloy or SK material. These lead to improved life and contact stability
Common problems of LGA Test socket Issues
Since LGA Test sockets need to keep stable performance even in harsh environments, it is necessary to incorporate measures to avoid troubles in advance by utilizing simulation technology. Here are common problems and solutions when using sockets for LGA Test sockets
Issues #1
Requirement for High frequency band
LGA Test sockets are often required to support high speed signal measurements. However, since the characteristics of normal contact pins do not correspond to the high frequency band, it is necessary to adopt contact pins that meet the required specifications.
Solutions
Use Capsule contact pin, which has short total length!
Use Coaxial contact pins, which is impedance-matched!
Issues #2
Requirement for durability
Durability is important because LGA Test socket is used repeatedly. Since the standard contact pin is made of Au plated beryllium copper, the plating on the pin tip is subject to wear out and Sn adhesion when used repeatedly, resulting in poor contact.
Solutions
Avoid pin wear by using palladium plating and SK material!
Avoid Sn adhesion by using carbon coating!
Issues #3
Requirement for low resistance measurement
LGA Test sockets are often required to support low resistance. However, some of the characteristics of normal contact pins do not support low resistance, so it is necessary to use contact pins that meet the required specifications.
Solutions
Achieve low resistance by shortening the pin length.
LGA socket
Solutions
-
Spring Probe Pin
Enplas's own design will provide internal short circuit of probe pin with low resistance value (Ave 50m ohm or under)
Enplas provides suitable socket design proposal to meet required specification -
Test socket with heat pipe
The high heat dissipation capacity enabled by the heat pipe's thermal circulation structure allows for the measurement of devices with high-heat-emitting packages.
-
Conductivity Carbon Coating
Achieved a significant longer life of contacts by preventing solder migration
Achieved high durability with high slidablity and hardness -
Capsule contact
The short-length probe pin structure (total length 1.5 mm) realizes good high-frequency characteristics.
Ideal for high-speed transmission and low-voltage products -
ES Plating
By developing special plating (ES plating), the life of burn-in socket contacts has been extended in high temperature environments.
Maintenance costs have also been significantly reduced by reducing re-gold plating costs, etc.
Our lineup of LGA sockets for Test Lineup
Socket | Pitch | Pin length | Operation Temperature | Lifetime | Load | Load |
---|---|---|---|---|---|---|
Press Probe | 0.8mm | 3.4mm | -55℃ ~ +120℃ | 200,000 times | 30gf | >20GHz at -1dB / >20GHz at -10dB |
4.2mm | -55℃ ~ +120℃ | 200,000 times | 22gf | 17.4GHz at -1dB / 14.5GHz at -10dB | ||
Capsule Pin Probe Pin | 0.5mm | 3.45mm | -55℃ ~ +125℃ | 200,000 times | 25gf | >20GHz at -1dB / >20GHz at -10dB |
0.8mm | 1.5mm | -55℃ ~ +125℃ | 250,000 times | 25gf | >20GHz at -1dB / >20GHz at -10dB | |
0.8mm | 3.3mm | -55℃ ~ +125℃ | 200,000 times | 25gf | >20GHz at -1dB / >20GHz at -10dB | |
0.5mm | 3.45mm | -55℃ ~ +125℃ | 200,000 times | 25gf | >20GHz at -1dB / >20GHz at -10dB | |
0.4mm | 3.75mm | -55℃ ~ +125℃ | 1,000,000 times | 25gf | >20GHz at -1dB / >20GHz at -10dB |
Please feel free to contact us with
your questions regarding test sockets.
Contact Us
- Is it possible to manufacture a socket with more than 10,000 pins?
- I am considering an electrical inspection methods for LGA ceramic packaging (20 to 50 mm) with several thousand pins. Do you have a suitable socket for this device?
- Can the BGA socket support ultra-fine pitch?
- What kind of analysis can you provide ?
- Is there export to overseas and get local support?
- What should I do if there is a problem?
- What is the guaranteed cycle?
- What temperature can it be used in?
- I would like to consider Enplas’s test socket. What kind of information I need to provide ?
- How long does it take to deliver?