For mass-produced burn-in, select the open-top type when using an automatic insertion / extraction machine to move the device in and out by machine, and select the clamshell type when inserting / removing by hand for reliability burn-in or performance evaluation.
Image sensor socket for burn-in
Supported Packages
-
Burn-in Sockets
Reliability Assessment /
For Mass Production -
Test Sockets
Property Assessment /
For Mass Production
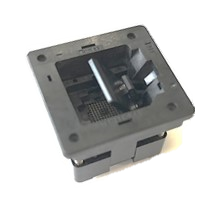
For burn-in test image sensor sockets, it is necessary to consider solutions for image sensor-specific requirements such as daylighting, anti-reflection, scratch prevention on the PKG glass surface, and dust adhesion prevention. Enplas Semiconductor Peripheral Corporation, which operates IC Socket Solutions.com, has various solutions that can handle these problems. In terms of cost, when testing the same PKG in large quantities in mass production burn-in or reliability burn-in, we can minimize the total cost with molded products, and in the case of special PKG or small-quantity testing, we can also handle machining socket option without incurring initial cost. It is possible to provide socket design options flexibly. In addition, it is also possible to take measures against heat generation of large sensors that consume large amounts of power and use contact pins with excellent electrical characteristics.
Points for selecting an image sensor socket for burn-in Points
For the socket for the image sensor for burn-in, it is necessary to select the appropriate socket specifications according to the test method, environment, and important functions. Here, we will introduce the important points in determining the specifications of the socket for the image sensor for burn-in.
Point#1
Select either open top or clamshell from the method of setting the device
Point#2
Select the most suitable contact pin specifications according to the type of PKG
For BGA, select the pinch contact pin or bottom contact pin, and for LGA, select the bottom contact pin.
Point#3
Examining the presence or absence of a lighting test and socket specifications
For image sensors that require a lighting test, select a socket with a lighting window or an open top socket. An open top socket with a lid is recommended if you want to avoid dust adhesion and scratches
Point#4
If power consumption is high and heat is high, select a socket specification that takes heat dissipation into consideration.
The image sensor, which consumes a lot of power and generates a lot of heat, realizes a stable burn-in test by adopting a socket with a heat sink on the back side.
Image sensor socket for burn-in common problems Issues
Since the socket for the image sensor for burn-in needs to show stable performance even in a harsh environment, it is necessary to incorporate measures to avoid troubles in advance by utilizing simulation technology. Here are some common problems and solutions for using sockets for burn-in image sensors.
Issue #1
I am worried about the adhesion and scratches of dust on the PKG glass surface during the test.
If dust in the burn-in equipment adheres to the PKG glass surface during mass production burn-in, accurate test results cannot be obtained and the PKG glass surface may be scratched.
Solutions
Uses an open top socket with a lid!
Issue #2
The heat generated by the device is large and stable measurement cannot be performed.
The temperature inside the burn-in oven varies greatly depending on the location, and among the image sensors, the large sensor, which consumes a particularly large amount of power, generates a large amount of heat from the device itself. Therefore, stable measurement cannot be performed by the burn-in test unless a socket with proper measures against heat generation is selected.
Solutions
Utilize thermal analysis simulation and avoid with the suitable socket with back heat sink!
The individual temperature control system can control the temperature of the device for each socket.
Issue #3
Repeated burn-in reduces device yield.
For Au-plated contact pins, the base of the contact pin may be exposed as the burn-in process is repeated. If this happens, the tin plating on the PKG lead will be transferred and peeled off, and the contact between the socket (contact pin) and the device will be poor. As a result, the burn-in test will be failed or the yield with the device will decrease.
Solutions
ES plating will bring a longer lifespan.
Image sensor socket for burn-in
Supported Packages
Burn In socket lineup for Image Sensor Solutions
IC Socket Solutions.com offers socket solutions that apply a bulit experience and simulation technology to all the challenges that arise when burn-in testing Image Sensor
-
Spring Probe Pin
Enplas's own design will provide internal short circuit of probe pin with low resistance value (Ave 50m ohm or under)
Enplas provides suitable socket design proposal to meet required specification -
Non-magnetic Socket
Non-magnetic socket will be required for sensor application
Corrosion resistance with non-magnetic performance -
Open top BGA two contact socket
Stable contact performance due to (two-point contact) structure
Double door structure makes it easy to insert PKG -
LCF series (general-purpose molded frame)
Low price and quick delivery for various devices up to 100mmx100mm
Replacible on site by surface mounting method -
Open Top Socket with Cover
Open top socket integrated with a mechanism that protects the entire top surface of the PKG.
Socket with cover to prevent dust in the air from coming into the socket. -
Socket with heat sink
Heat Sink will reduce the increase of device temperature by contacting device surface with this parts and radiating the device heat into the air.
-
Individual Temparature Control System
Heater and temperature sensors can be attached to control the temperature of the device for each socket.
Achieves more accurate temperature control in comparison with general burn-in equipment (temperature setting ± 3 ° C) -
ES Plating
By developing special plating (ES plating), the life of burn-in socket contacts has been extended in high temperature environments.
Maintenance costs have also been significantly reduced by reducing re-gold plating costs, etc. -
AM contact series
Low price and quick delivery for various devices by using machined Contact unit
Replacible on site by surface mounting method
Please feel free to contact us with
your questions regarding burn-in sockets.
Contact Us
- Is it possible to manufacture a socket with more than 10,000 pins?
- I am considering an electrical inspection methods for LGA ceramic packaging (20 to 50 mm) with several thousand pins. Do you have a suitable socket for this device?
- Is it possible to support high pins counts of BGA socket?
- How do you prevent the BGA heating with the socket ?
- Can the BGA socket support ultra-fine pitch?
- What kind of analysis can you provide ?
- Is there export to overseas and get local support?
- What should I do if there is a problem?
- What is the guaranteed cycle?
- What temperature can it be used in?
- I would like to consider a burn-in socket, but what information do you need?
- How long does it take to deliver?
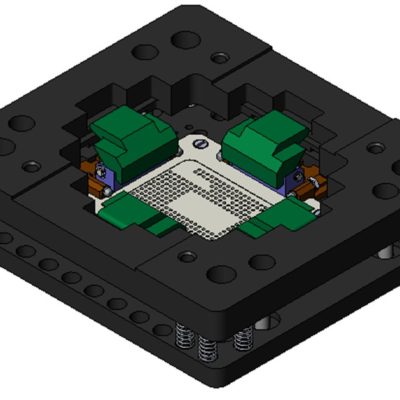
Sockets for test image sensors are required to have a pressing structure that must avoid scratches on the top surface of the PKG, but at Enplas Semiconductor Peripheral Corporation, which operates IC Socket Solution.com, recommends double latch type socket or clamshell type socket for characterization. For mass production tests, we have sockets that can be used with latch pressing type. Furthermore, for mass production testing, we have all the solutions in the final test process of the image sensor, such as a positioning mechanism that can flexibly respond to the dimensional variation especially for ceramic PKG, and also low contact force probe pins to reduce the pressing load.
Points for selecting an image sensor socket for test Points
For the socket for the image sensor for test, it is necessary to select the appropriate socket specifications according to the test method, environment, and important functions. Here, we introduce the important points in determining the specifications of the socket for the image sensor for test.
Point#1
Select the socket mechanism according to the test environment and purpose
When using a socket for a test image sensor in a mass production test, select the latch pressing type or the type without a pressing mechanism. If you want to use it for manual evaluation, select double latch type or clamshell type. The cover of the double latch type can be removed.
Point#2
If you need to handle high frequencies, select a high-frequency pin accordingly
If high frequency characteristics are required, select a pin that provides good insertion loss and return loss, such as capsule contact socket and coaxial contact pin.
Point#3
Use a low contact force probe when the pressing load is limited
When the pressing load is limited due to the pressing area or device restrictions, the contact stability is improved by adopting a low contact force probe.
Image sensor socket for test common problems Issues
Since the socket for the test image sensor needs to show stable performance even under severe conditions, it is necessary to incorporate measures to avoid trouble in advance according to the expected phenomena. Here are some common problems and solutions when using sockets for test image sensors.
Issue #1
I am troubled by dimensional variation of ceramic PKG, wear, and scratches on the glass surface due to latches.
In general, ceramic PKGs have large dimensional variations, and positioning accuracy cannot be achieved with ordinary IC sockets. In addition, burrs of the ceramic PKG is accumulated and adhered to the socket or PKG, or interference between the socket guide and the PKG causing scraps, which leads to deterioration of positioning accuracy. Furthermore, due to the latch pressing, the wiping on the upper surface of the glass will be scratched and damaged.
Solutions
Solve with a specialized socket designed for image sensor.
Issue #2
I want to evaluate performance with high-performance pin
Since the image sensor needs to be tested in severe testing environment, evaluation with a pin with low inductance will lead to an improvement in yield even in the test process.
Solutions
Use capsule contact・ and coaxial probe.
Issue #3
Pressing area and pressing load are limited
When the PKG pressing area is limited even with high contact force pins from the back side, it is not able to press the entire PKG. In addition, if the pressing load cannot be increased due to device restrictions, it will lead to poor contact and an accurate test cannot be performed.
Solutions
The solution is to use a low contact force probe pin.
Image sensor socket for burn-in
Supported Packages
Test socket lineup for Image Sensor Solutions
IC Socket Solutions.com offers socket solutions that apply a bulit experience and simulation technology to all the challenges that arise when final testing Image Sensor
-
Spring Probe Pin
Enplas's own design will provide internal short circuit of probe pin with low resistance value (Ave 50m ohm or under)
Enplas provides suitable socket design proposal to meet required specification -
Conductivity Carbon Coating
Achieved a significant longer life of contacts by preventing solder migration
Achieved high durability with high slidablity and hardness -
ES Plating
By developing special plating (ES plating), the life of burn-in socket contacts has been extended in high temperature environments.
Maintenance costs have also been significantly reduced by reducing re-gold plating costs, etc.
Please feel free to contact us with
your questions regarding test sockets.
Contact Us
- Is it possible to manufacture a socket with more than 10,000 pins?
- Are there sockets for writing program data?
- I am considering an electrical inspection methods for LGA ceramic packaging (20 to 50 mm) with several thousand pins. Do you have a suitable socket for this device?
- Is it possible to support high pins counts of BGA socket?
- Is it possible to support high frequencies in the BGA test socket?
- Can the BGA socket support ultra-fine pitch?
- What kind of analysis can you provide ?
- Is there export to overseas and get local support?
- What should I do if there is a problem?
- What is the guaranteed cycle?
- What temperature can it be used in?
- I would like to consider Enplas’s test socket. What kind of information I need to provide ?
- How long does it take to deliver?