Auto loading machine → Open top
Manual operation → Clam Shell
Socket for Power Device
Supported Packages
-
Burn-in Sockets
Reliability Assessment /
For Mass Production -
Test Sockets
Property Assessment /
For Mass Production
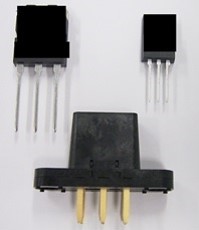
The burn-in socket for Power device is an inexpensive socket made of molded method.
In order to achieve high contact reliability, there is a two-point contact solution that sandwich the tip of package lead. There are also bottom contact pin options that enable to contact multiple pin for high current solutions. We can also provide that Heatsink option for heat dissipation purpose.
Selecting points for power device for burn-in Points
For power device sockets, it is important to select based on the usage and environment.
We introduce the key points to determine the specifications of the Power device for burn-in usage.
Point#1
Select either open top or clamshell based on method of setting the device.
Point#2
Select the mounting method on the board by either focusing on contact reliability or focusing on maintainability.
Select the solder mounting method if you want to emphasize the contact reliability between the socket and the board, and select the surface mount method if you want to emphasize maintainability.
Solder mounting method / Emphasis on contact reliability
Using 2 points pinch type pin with above 0.65mm pitch. BGA sockets are relatively inexpensive because they are mainly made with molded method.
Surface mount method / Emphasis on maintainability
Using bottom contact probe with vertical movement and more effective for Package warpage. Machined pin options available that enable to support the fine / multi pitch.
Point#3
Consider the method for heat dissipation and high current solutions.
We provide the most applicable heatsink style after running heat simulation. For high current solution, we are able to suggest bypass pin options as necessary.
Power Device for burn-in Common problems Issues
Power Device socket for burn-in require to have stable performance even in a harsh environment, it is necessary to incorporate measures to avoid troubles in advance by utilizing simulation technology. Here are some common problems you may have when using BGA sockets for burn-in and solutions to them.
Issue #1
Difficult to find the general purpose socket due to special / unique pacakge shape
Since many Power devices are special and large compared to other ICs, general-purpose sockets cannot be applied and the cost tends to be higher
Solutions
We can design the contact unit with machined based on the Package shaepe, and utlize the molded frame with AM pin which allows to reduce intial socket manufacture cost.
Issue #2
Improve the thermal dissipation due to over heating.
Power devices generate a lot of heat and can cause thermal runaway during burn-in tests if they do not dissipate heat efficiently.
Solutions
We will provide the thermal simulation and able to provide the individual heat control system to resolve the issue.
Issue #3
Repeated burn-in testing reduces yield
For Au-plated contact pins, the base material of the contact pin may be exposed as the burn-in process is repeated. If this happens, the tin plating on the PKG Pad will be peeled off and transferred, and the contact between the socket (contact pin) and the device will become poor. As a result, the burn-in test will be NG and the yield with the device will decrease.
Solutions
Achieves a long life with contact pins that use ES plating.
Socket for Power Device
Supported Packages
Burn In socket lineup for Power Device Solutions
IC Socket Solutions.com offers socket solutions that apply a bulit experience and simulation technology to all the challenges that arise when burn in testing Power Device
-
High-Frequency Socket for System-Level Testing
Enhanced Grounding and Excellent High-Frequency Characteristics Achieved by Plating the Housing
Supports PAM4 Serdes 112Gbps Operation -
High Pin Count Solutions
Achieves stable contact performance and long life.
High current capacity is possible with integrated springs. -
QFP/SOP Open Top Socket with Ground Pins
Stable Contact Performance with Cantilever Structure (2-Point Contact)
Ground Pins for Continuity Testing and Heat Dissipation Pins for High-Heat Packages -
Open Top QFP/SOP pinch type socket
Pinch type contact (2-point contact) makes stable contact
Contact pin surface cleaning function prevents from accumulating debris due to the step between the bottom pin and the molded body surface. -
Sockets for power devices
Compatible with various power devices that are not handled by other companies
It is also possible to consider the optimum pin arrangement and support large currents of power devices. -
Socket with heat sink
Heat Sink will reduce the increase of device temperature by contacting device surface with this parts and radiating the device heat into the air.
-
Individual Temparature Control System
Heater and temperature sensors can be attached to control the temperature of the device for each socket.
Achieves more accurate temperature control in comparison with general burn-in equipment (temperature setting ± 3 ° C) -
ES Plating
By developing special plating (ES plating), the life of burn-in socket contacts has been extended in high temperature environments.
Maintenance costs have also been significantly reduced by reducing re-gold plating costs, etc. -
AM contact series
Low price and quick delivery for various devices by using machined Contact unit
Replacible on site by surface mounting method
Please feel free to contact us with
your questions regarding burn-in sockets.
Contact Us
- Can you make sockets for unique, custom-made packages?Since the socket will be used for System Level Testing, devices will be tested in high volume and it is important that the devices can be easily placed and removed.
- What kind of analysis can you provide ?
- Is there export to overseas and get local support?
- What should I do if there is a problem?
- What is the guaranteed cycle?
- What temperature can it be used in?
- I would like to consider a burn-in socket, but what information do you need?
- How long does it take to deliver?
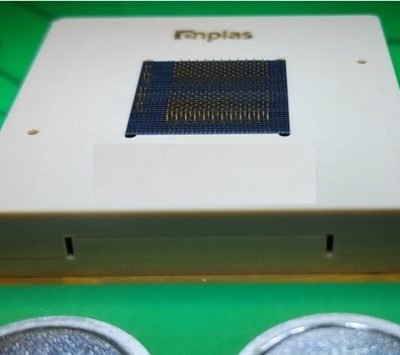
Test sockets for Power devices contact the lead terminals to ensure a secure electrical connection.
A probe pin and a press pin are used as contacts, making it possible to dissipate heat with a heat sink. We also offer models that use a surface pressure connection method that is easy to maintain.
The leaf spring contactor for wafer and chip testing have 4 point crown and ensures stable contact performance. Also, low contact force and low wiping technology enable to reduce the marking on the PAD side.
Furthermore, we enable cost reduction by combining molded housing and a machined socket frame. Since the molded housing is removable, replacement can be done easily at site.
Selecting points for power device for burn-in Points
For power device sockets, it is important to select based on the usage and environment.
We introduce the key points to determine the specifications of the Power device for Test Socket usage.
Point#1
Select the socket type based on Mold PKG, or Chip / Wafer
Regular test socket can be used if mold PKG type.
Chip contactor can be used if Chip / Wafer contact
Point#2
Determine the number of contact pins to contact according to the amount of current in the device
Since the allowable current for one contact pin is limited, the number of pins to be contacted with the terminal is determined according to the amount of current of the Power device.
Point#3
If heat dissipation is required, consider using a heat sink
Power devices, which are often designed on the premise of heat dissipation, can be simulated in advance when considering a test socket. Having heat sink on the socket will enable the stable test performance.
Power Device for Test Common problems Issues
Since test sockets for Power devices need to exhibit stable performance even in harsh environments, it is necessary to incorporate measures to avoid troubles in advance by utilizing simulation technology. Here are some common problems and solutions for using test sockets for Power devices.
Issue #1
Want to performed testing wafer / chip sate with high current.
Want to performed testing wafer / chip sate with high current.
Solutions
Many contact pins can be contacted with one PAD to handle large currents by using the chip contactor.
Issue #2
I want to test with the chip temperature controlled
When testing multiple Power devices, it is not possible to perform accurate tests such as thermal runaway due to heat generation.
Solutions
By utilizing individual temperature control, it is possible to monitor the PKG surface temperature and operate it in combination with a heater and FAN to keep it at any temperature.
Socket for Power Device
Supported Packages
Test socket lineup for Power Device Solutions
IC Socket Solutions.com offers socket solutions that apply a bulit experience and simulation technology to all the challenges that arise when testing Power Device
-
High-voltage (10,000V) insulation test socket.
The high-voltage test socket supports up to 10,000V and features developed large-stroke press and probe pins. We also offer a variety of contacts for different currents and can provide custom solutions.
-
IGBT Test Socket
Stable contact performance (1000A) with high current terminals for AC/DC testing. Reduced contact marks and high durability with press contacts for insulation testing.
-
High-Frequency Socket for System-Level Testing
Enhanced Grounding and Excellent High-Frequency Characteristics Achieved by Plating the Housing
Supports PAM4 Serdes 112Gbps Operation -
High Pin Count Solutions
Achieves stable contact performance and long life.
High current capacity is possible with integrated springs. -
Spring Kelvin Contact
Achieves stable contact performance and long life.
High current capacity is possible with integrated springs. -
Chip Contactor
Huge cost reduction of chip contactor which supports high current with tooled contact pin and contact module
Moduled contact pin related component makes it easier to exchange the parts on site. -
Conductivity Carbon Coating
Achieved a significant longer life of contacts by preventing solder migration
Achieved high durability with high slidablity and hardness -
ES Plating
By developing special plating (ES plating), the life of burn-in socket contacts has been extended in high temperature environments.
Maintenance costs have also been significantly reduced by reducing re-gold plating costs, etc.
Please feel free to contact us with
your questions regarding test sockets.
Contact Us
- Can you make sockets for unique, custom-made packages?Since the socket will be used for System Level Testing, devices will be tested in high volume and it is important that the devices can be easily placed and removed.
- What kind of analysis can you provide ?
- Is there export to overseas and get local support?
- What should I do if there is a problem?
- What is the guaranteed cycle?
- What temperature can it be used in?
- I would like to consider Enplas’s test socket. What kind of information I need to provide ?
- How long does it take to deliver?