Open top type will be chosen by auto loading system, and clam shell type will be chosen by manual loading.
QFP Socket
-
Burn-in Sockets
Reliability Assessment /
For Mass Production -
Test Sockets
Property Assessment /
For Mass Production
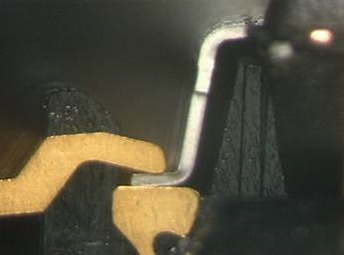
QFP socket for burn-in provides electrical contact on QFP terminal with contactor. We have 2 types of contactor, one is pinch contact on lead terminal, the other is probe-pin type. For open top type socket, we have the design of pinch contact type (good contact performance), contact point cleaning function, or solution for reducing solder scrap (molding parts and contact pin gap will prevent solder scrap).
Enplas also provides thermal solution for high heat device.
Selecting points for QFP Socket for burn-in Points
For burn-in sockets, it is important to select based on the usage and environment.
We introduce the key points to determine the specifications of the QFP Socket for burn-in usage.
Point#1
Choose open top type or clam shell type by device loading method
Point#2
Decide device quide type
Mod guide will be used for tight and stable positioning of the device. Lead guide will be used for flexible device type (different package thickness) or versatility.
Point#3
Consider heat radiation or high current compatibility
Mod guide will be used for tight and stable positioning of the device. Lead guide will be used for flexible device type (different package thickness) or versatility.
QFP Socket for burn-in Common problems Issues
Since the QFP Socket for burn-in require to have stable performance even in a harsh environment, it is necessary to incorporate measures to avoid troubles in advance by utilizing simulation technology. Here are some common problems you may have when using QFP Sockets for burn-in and solutions to them.
Issues #1
Thermal runaway happens by self heat generation of the device
There is the case of thermal runaway under high temperature of burn in test in case of the high heat generaiton device. If it happens, we can not run burn in test after that.
Solutions
Heat sink will be good option based on thermal simulation
Issues #2
Package get the damage due to repeated burn in test.
The socket goes throuh repeated burn-in test, then solder scrap will be generated, and it brings defect of appearance in some cases. In addition, package will stuck during insettion by solder scrap
Solutions
Enplas provides wiping solution of solder scrap based on our enough experience of burn-in socket
Issues #3
Yeild of burn in test get worse after repeated burn in process
In case of Au plating contact pin in the socket,the base metal of contact pin will be exposed after repeated burn-in process. In such condition, Sn plating of lead on the device is removed and transferred, then it bring bad contact between socket (contact pin) and package. As a result, NG of burn in test occures and it brings lower yield of BI test process.
Solutions
ES plating technology will bring longer socket life
QFP Socket
Solutions
-
High-Frequency Socket for System-Level Testing
Enhanced Grounding and Excellent High-Frequency Characteristics Achieved by Plating the Housing
Supports PAM4 Serdes 112Gbps Operation -
High Pin Count Solutions
Achieves stable contact performance and long life.
High current capacity is possible with integrated springs. -
QFP/SOP Open Top Socket with Ground Pins
Stable Contact Performance with Cantilever Structure (2-Point Contact)
Ground Pins for Continuity Testing and Heat Dissipation Pins for High-Heat Packages -
Spring Probe Pin
Enplas's own design will provide internal short circuit of probe pin with low resistance value (Ave 50m ohm or under)
Enplas provides suitable socket design proposal to meet required specification -
Non-magnetic Socket
Non-magnetic socket will be required for sensor application
Corrosion resistance with non-magnetic performance -
Open Top QFP/SOP pinch type socket
Pinch type contact (2-point contact) makes stable contact
Contact pin surface cleaning function prevents from accumulating debris due to the step between the bottom pin and the molded body surface. -
Custom socket for high power liquid cooling system
Not only BGA, and LGA, but also various type of package including QFN can be designed by using a socket that is suitable for the thermal head size
-
LCF series (general-purpose molded frame)
Low price and quick delivery for various devices up to 100mmx100mm
Replacible on site by surface mounting method -
Sockets for power devices
Compatible with various power devices that are not handled by other companies
It is also possible to consider the optimum pin arrangement and support large currents of power devices. -
Socket with heat sink
Heat Sink will reduce the increase of device temperature by contacting device surface with this parts and radiating the device heat into the air.
-
Individual Temparature Control System
Heater and temperature sensors can be attached to control the temperature of the device for each socket.
Achieves more accurate temperature control in comparison with general burn-in equipment (temperature setting ± 3 ° C) -
Super Shrink Socket
Increase of BIB density (1.8 times better density rate per 1 BIB)
In the condition of same socket qty, the reduction of BIB qty (45% reduction) -
ES Plating
By developing special plating (ES plating), the life of burn-in socket contacts has been extended in high temperature environments.
Maintenance costs have also been significantly reduced by reducing re-gold plating costs, etc. -
AM contact series
Low price and quick delivery for various devices by using machined Contact unit
Replacible on site by surface mounting method
QFP Burn-in Socket Line up Enplas offers Lineup
Socket | Pitch | 16pin | 24pin | 32pin | 44pin | 48pin | 52pin | 64pin | 68pin | 70pin | 80pin | 92pin | 100pin | 112pin | 116pin | 118pin | 120pin | 128pin | 132pin | 144pin | 164pin | 172pin | 176pin | 196pin | 208pin | 216pin | 256pin |
---|---|---|---|---|---|---|---|---|---|---|---|---|---|---|---|---|---|---|---|---|---|---|---|---|---|---|---|
Open Top | 0.4mm | #bg# | |||||||||||||||||||||||||
0.5mm | #bg# | ||||||||||||||||||||||||||
0.635mm | #bg# | ||||||||||||||||||||||||||
0.65mm | #bg# | ||||||||||||||||||||||||||
0.8mm | #bg# | ||||||||||||||||||||||||||
1.0mm | #bg# | ||||||||||||||||||||||||||
Clam Shell | 0.4mm | #bg# | |||||||||||||||||||||||||
0.5mm | #bg# | ||||||||||||||||||||||||||
0.635mm | #bg# | ||||||||||||||||||||||||||
0.65mm | #bg# | ||||||||||||||||||||||||||
0.8mm | #bg# | ||||||||||||||||||||||||||
1.0mm | #bg# | ||||||||||||||||||||||||||
1.27mm | #bg# |
Please feel free to contact us with
your questions regarding burn-in sockets.
Contact Us
- Is it possible to manufacture a socket with more than 10,000 pins?
- Do you have any solutions for heat dissipation?
- Can you support burn-in at temperatures above 150℃?
- Do you have any solution for improving contact performance?
- What kind of analysis can you provide ?
- Is there export to overseas and get local support?
- What should I do if there is a problem?
- What is the guaranteed cycle?
- What temperature can it be used in?
- I would like to consider a burn-in socket, but what information do you need?
- How long does it take to deliver?
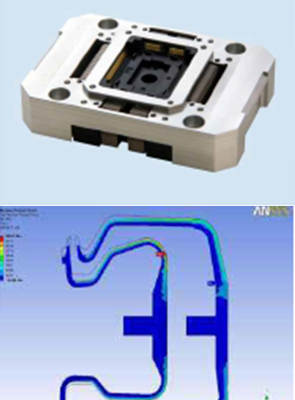
QFP socket for test purpose requires especially long life time and high current capability. If electristic characteristic is required, we use short-length probe pin for kelvin test under high current situation. Furthermore, hard Pb alloy will be selected for long life time of contactor, and, surface mount type press kelvin contact pin will be used for stable contact performance and long life. Because press kelvin contact pin is for surface mount type socket, it is easy to exchange pin into new one after deterioration of pin and it is good fit for mass production test purpose.
Enplas will offer good solution for the requirement on QFP test socket.
Selecting points for QFP test socket for burn-in POINTS
For burn-in sockets, it is important to select based on the usage and environment.
We introduce the key points to determine the specifications of the QFP test socket for burn-in usage.
Point1
Choose the suitable contact pin to meet the customer requirement/spec
We choose the suitable contact pin based on customer requirement/spec; for example, probe pin for electric characteristic, press pin for high current/high temperature requirement or cost effective solution.
Point2
For stable contact performance, pin tip shape or stroke amount can be adjusted
The more contact tip the pin has, the better contact performance the pin has. 4 point contact tip has cost effective solution, and 6 or 8 point contact tip has better contact performance. Also, we choose the pin which the stroke can be adjusted based on equipment type.
Point3
Choose the material of contact pin tip based on required life time
In order to increase the abrasion resistance, we have several solution. Carbon coating on pin tip or change of the material on pin tip into Pd alloy or carbon tool steel material (SK material) will bring better abrasion resistance or stabe contact performance with avoiding Sn waste on pin tip.
QFP test socket for burn-in Common problems Issues
Test socket is expected to have stable performance under severe usage condition, so, we need to be prepared well in order to avoid the trouble which can be assumed in advance using simulation technology. Here, we provide the case study and counter measure for that.
Issues #1
Want to increase the durabitliy of socket
It is important to have good durabitiliy for QFP test socket due to repeated usage. Standard contact pin has Au plating on beryllium copper. After many usage of the socket, pin tip will wear or Sn waste will stick to pin tip, and it will casue contact problem.
Solutions
Avoid the wear of contact pin with Pd plating or carbon tool steel material (SK material)
Avoid the contact deterioration by Sn waste on pin tip using carbon coating
Issues #2
Charasteristic of fine signa can not be evaluated correctly
In electristic characteristic test, we need to check if the device works under fine signal condition. Usual contact pin of test socket has the difficulty in right evaluation of fine signal because it can not prevent the increase of resistance value.
Solutions
Kelvin contact pin (Probe type or press type) can omit the effect on package characteristic.
Issues #3
contact performance is not stable due to package dimension dispersion
It is easy to bring the contact problem due do dispersion of package dimension because this will cause unstable device location in the socket. In such case, contact margin will be increased and absorb such dimension dispersion in QFP socket
Solutions
Muitiple pin tip solution will solve contact problem
Issues #4
We want the test socket compatible for high current.
For QFP package, we have the case of high current such as 10A per 1 pin, but usual contact pin will not meet this condition. So, we need to choose the contact pin which is compatilbe with high current.
Solutions
Press Kelvin contact pin is compatible with high current.
It will bring stable contact performance and long life time, too.
QFP Socket
Solutions
-
High-Frequency Socket for System-Level Testing
Enhanced Grounding and Excellent High-Frequency Characteristics Achieved by Plating the Housing
Supports PAM4 Serdes 112Gbps Operation -
High Pin Count Solutions
Achieves stable contact performance and long life.
High current capacity is possible with integrated springs. -
Spring Kelvin Contact
Achieves stable contact performance and long life.
High current capacity is possible with integrated springs. -
Spring Probe Pin
Enplas's own design will provide internal short circuit of probe pin with low resistance value (Ave 50m ohm or under)
Enplas provides suitable socket design proposal to meet required specification -
Conductivity Carbon Coating
Achieved a significant longer life of contacts by preventing solder migration
Achieved high durability with high slidablity and hardness -
Capsule contact
The short-length probe pin structure (total length 1.5 mm) realizes good high-frequency characteristics.
Ideal for high-speed transmission and low-voltage products -
ES Plating
By developing special plating (ES plating), the life of burn-in socket contacts has been extended in high temperature environments.
Maintenance costs have also been significantly reduced by reducing re-gold plating costs, etc.
QFP Test Socket Sine up Enplas offers Lineup
Pitch | Operation Temperature | Lifetime | Load | Contact Resistance | Current | |
---|---|---|---|---|---|---|
Press Kelvin | 0.4mm | -65℃~150℃ | 500,000 times | 45gf | 100mΩ | 8A |
0.5mm | ||||||
0.65mm | ||||||
0.8mm | ||||||
1.0mm | ||||||
1.27mm |
pitch | Operation Temperature | Lifetime | Load | Insertion Loss/ Reflection Loss | |
---|---|---|---|---|---|
Capsule Pin | 0.5mm | -55℃ ~ +125℃ | 200,000 times | 25gf | >20GHz at -1dB / >20GHz at -10dB |
0.8mm | 250,000 times | ||||
Probe Pin | 0.8mm | 200,000 times | |||
0.5mm | 200,000 times | ||||
0.4mm | 1,000,000 times |
Please feel free to contact us with
your questions regarding test sockets.
Contact Us
- Is it possible to manufacture a socket with more than 10,000 pins?
- Do you have any solutions for heat dissipation?
- Can you support burn-in at temperatures above 150℃?
- Are there sockets for writing program data?
- What kind of analysis can you provide ?
- Is there export to overseas and get local support?
- What should I do if there is a problem?
- What is the guaranteed cycle?
- What temperature can it be used in?
- I would like to consider Enplas’s test socket. What kind of information I need to provide ?
- How long does it take to deliver?