Select the open top type when inserting and removing devices with an automatic insertion / removal machine such as mass production BI, and select the clamshell type when inserting and removing by hand for reliability BI and performance evaluation.
Burn-in socket for Sensor devices
Supported Packages
-
Burn-in Sockets
Reliability Assessment /
For Mass Production -
Test Sockets
Property Assessment /
For Mass Production
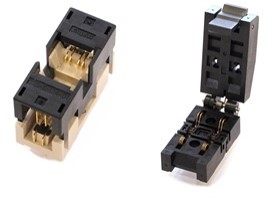
Burn-in (BI) socket for Sensor devices can be applied to a wide variety of devices because various molded parts are available at a low price without incurring initial costs, when it is used at high volume for either mass production burn-in or reliability burn-in. When it is used for characteristic evaluation of specially designed PKG at small-quantity, machined parts are used to avoid incurring initial costs. Also, it can be designed for non-magnetic, high current, ultra-low voltage, etc. that are unique to sensor devices. There are also multi-mounted sockets that can inspect many PKGs with one socket for sensor devices with relatively small PKG sizes.
Key points for selecting a BI socket for Sensor devices Points
For BI socket for Sensor devices, it is necessary to select the optimum specifications depending on the usage, environment, and the function of device. Here are important points in determining the specifications of BI socket for Sensor devices
Point#1
Select the method of setting the device from either open top or clamshell
Point#2
Select the most suitable contact pin specifications according to the type of PKG
For BGA, pinch contact pin / bottom contact pin, for LGA, bottom pad type, for QFN, bottom pad type (leaf spring / probe), for SOP / QFP, leaf spring 2-point contact type / bottom pad.
Point#3
Use a special socket according to the function of the sensor
Select the optimum socket specifications according to the sensor function. For example, a non-magnetic socket for a magnetic sensor and a socket with a lighting window for an optical sensor.
Common problems of BI socket for Sensor devices Issues
Since BI socket for Sensor devices need to keep stable performance even in harsh environments, it is necessary to incorporate measures to avoid troubles in advance by utilizing simulation technology. Here are common problems and solutions when using sockets for BI socket for Sensor devices
Issue #1
The socket is magnetized and affects the measurement result.
The metal parts of a standard IC socket will be magnetized in the evaluation and inspection of the magnetic sensor, and accurate results will not be obtained.
Solutions
Non-magnetic socket will solve the issue of magnetization
Issue #2
Error occurs when detecting a small amount of current
Especially for sensors, it is important to measure and inspect low current and low voltage, but the expected results may not be obtained due to the influence of the contact resistance of the contact pins.
Solutions
Adopting ES plating prevent peeling of contact pin plating, exposure and oxidation of the base to prevent increase in resistance value.
Uses a Kelvin contact, which can reliably evaluate minute signal characteristics!
Issue #3
Difficult to obtain socket due to special PKG shape
Since many sensor ICs use special PKGs, they may not fit in general-purpose sockets.
Solutions
The AM contact series supports a wide variety of special PKGs in small quantities while keeping costs down!
Flexible sockets support special PKG shapes!
Burn-in socket for Sensor devices
Supported Packages
Burn In socket lineup for semiconductor sensor Solutions
IC Socket Solutions.com offers socket solutions that apply a bulit experience and simulation technology to all the challenges that arise when burn-in testing a semiconductor sensor
-
High-Frequency Socket for System-Level Testing
Enhanced Grounding and Excellent High-Frequency Characteristics Achieved by Plating the Housing
Supports PAM4 Serdes 112Gbps Operation -
High Pin Count Solutions
Achieves stable contact performance and long life.
High current capacity is possible with integrated springs. -
QFP/SOP Open Top Socket with Ground Pins
Stable Contact Performance with Cantilever Structure (2-Point Contact)
Ground Pins for Continuity Testing and Heat Dissipation Pins for High-Heat Packages -
Open Top QFP/SOP pinch type socket
Pinch type contact (2-point contact) makes stable contact
Contact pin surface cleaning function prevents from accumulating debris due to the step between the bottom pin and the molded body surface. -
Socket with heat sink
Heat Sink will reduce the increase of device temperature by contacting device surface with this parts and radiating the device heat into the air.
-
Individual Temparature Control System
Heater and temperature sensors can be attached to control the temperature of the device for each socket.
Achieves more accurate temperature control in comparison with general burn-in equipment (temperature setting ± 3 ° C) -
ES Plating
By developing special plating (ES plating), the life of burn-in socket contacts has been extended in high temperature environments.
Maintenance costs have also been significantly reduced by reducing re-gold plating costs, etc. -
AM contact series
Low price and quick delivery for various devices by using machined Contact unit
Replacible on site by surface mounting method
Please feel free to contact us with
your questions regarding burn-in sockets.
Contact Us
- Is it possible to manufacture a socket with more than 10,000 pins?
- Do you have any solutions for heat dissipation?
- Can you support burn-in at temperatures above 150℃?
- Can you make sockets for unique, custom-made packages?Since the socket will be used for System Level Testing, devices will be tested in high volume and it is important that the devices can be easily placed and removed.
- I am considering an electrical inspection methods for LGA ceramic packaging (20 to 50 mm) with several thousand pins. Do you have a suitable socket for this device?
- Do you have any solution for improving contact performance?
- Is it possible to support high pins counts of BGA socket?
- How do you prevent the BGA heating with the socket ?
- Can the BGA socket support ultra-fine pitch?
- What kind of analysis can you provide ?
- Is there export to overseas and get local support?
- What should I do if there is a problem?
- What is the guaranteed cycle?
- What temperature can it be used in?
- I would like to consider a burn-in socket, but what information do you need?
- How long does it take to deliver?
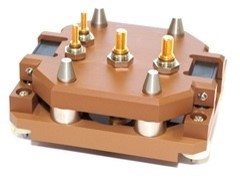
Semiconductor Sensor Socket for characteristics evaluation applys double latch type or clam shell type, and for mass production test purpose, latch pressure type will be used, too.
Enplas offers variety of solution for special parkage applicable socekt with precise machining technology, non-magnetic requirement for sensor device or high current/ ultra low voltage solution.
Test socket for Sensor devices Points
For Test socket for Sensor devices, it is necessary to select the optimum specifications depending on the usage, environment, and important functions. Here, we will introduce the important points in determining the specifications of Test socket for Sensor devices.
Point#1
Select the socket mechanism according to the test environment and purpose
When using a Test socket for Sensor devices in the mass production test, select the latch pressing type or the type without a pressing mechanism. If you want to use it for manual evaluation, select double latch type or clamshell type. The cover of the double latch type is removable.
Point#2
For testing high frequencies, select a high-frequency pin accordingly.
If high frequency characteristics are required, select pins that minimize insertion loss and return loss, such as capsule contact sockets and coaxial contact pins. If low resistance pins are required, such as low voltage operating products, select Kelvin contact.
Point#3
Use a special socket according to the function of the sensor
Select the optimum IC socket specifications according to the sensor function. For example, a non-magnetic socket for a magnetic sensor and an antireflection socket for an optical sensor.
Common problems of Test socket for Sensor devices Issues
Since Test socket for Sensor devices need to keep stable performance even in harsh environments, it is necessary to incorporate measures to avoid troubles in advance by utilizing simulation technology. Here are common problems and solutions when using Test socket for Sensor devices
Issue #1
Error occurs in low voltage / constant current measurement
Especially for sensors, it is important to measure and inspect low current and low voltage, but the expected results may not be obtained due to the influence of the contact resistance of the contact pins.
Solutions
Adopting ES plating prevent peeling of contact pin plating, exposure and oxidation of the base to prevent increase in resistance value.
Uses a Kelvin contact, which can reliably evaluate minute signal characteristics!
Issue #2
high-performance pins
To improve the yield in evaluating the sensitive performance of sensors, a pin with low loss and with low inductance is recommended.
Solutions
Uses Capsule contacts and Coaxial probes!
Issue #3
The socket is magnetized and affects the measurement result.
The metal parts of a standard IC socket will be magnetized in the evaluation and inspection of the magnetic sensor, and accurate results will not be obtained.
Solutions
Uses a non-magnetic socket to avoid magnetism
Burn-in socket for Sensor devices
Supported Packages
Test socket lineup for semiconductor sensor Solutions
IC Socket Solutions.com offers socket solutions that apply a bulit experience and simulation technology to all the challenges that arise when testing a semiconductor sensor
-
High-Frequency Socket for System-Level Testing
Enhanced Grounding and Excellent High-Frequency Characteristics Achieved by Plating the Housing
Supports PAM4 Serdes 112Gbps Operation -
High Pin Count Solutions
Achieves stable contact performance and long life.
High current capacity is possible with integrated springs. -
Conductivity Carbon Coating
Achieved a significant longer life of contacts by preventing solder migration
Achieved high durability with high slidablity and hardness -
ES Plating
By developing special plating (ES plating), the life of burn-in socket contacts has been extended in high temperature environments.
Maintenance costs have also been significantly reduced by reducing re-gold plating costs, etc.
Please feel free to contact us with
your questions regarding test sockets.
Contact Us
- Is it possible to manufacture a socket with more than 10,000 pins?
- Do you have any solutions for heat dissipation?
- Can you support burn-in at temperatures above 150℃?
- Are there sockets for writing program data?
- Can you make sockets for unique, custom-made packages?Since the socket will be used for System Level Testing, devices will be tested in high volume and it is important that the devices can be easily placed and removed.
- I am considering an electrical inspection methods for LGA ceramic packaging (20 to 50 mm) with several thousand pins. Do you have a suitable socket for this device?
- Is it possible to support high pins counts of BGA socket?
- Is it possible to support high frequencies in the BGA test socket?
- Can the BGA socket support ultra-fine pitch?
- What kind of analysis can you provide ?
- Is there export to overseas and get local support?
- What should I do if there is a problem?
- What is the guaranteed cycle?
- What temperature can it be used in?
- I would like to consider Enplas’s test socket. What kind of information I need to provide ?
- How long does it take to deliver?