Select the open top type when moving the device in and out by machine, and the clamshell type when inserting and removing it by hand.
Socket for burn-in MCU
Supported Packages
-
Burn-in Sockets
Reliability Assessment /
For Mass Production -
Test Sockets
Property Assessment /
For Mass Production
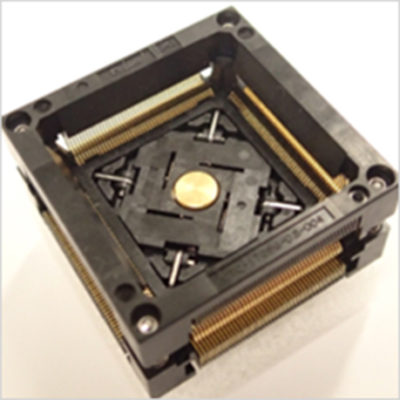
IC Socket Solution.com’s sockets for burn-in MCUs are inexpensive sockets made from molded products. A shoulder rest type that eliminates damage to the solder mounting surface of the PKG lead, or a two-point contact type that makes contact by sandwiching the tip of the PKG lead is available to achieve high contact reliability. If the PKG has a heat dissipation tab, a heat dissipation pin is also provided on the socket side to transfer heat to the board to dissipate heat, or to air-cool the heat dissipation pin for direct heat dissipation. We will solve all your worries when you burn in test your MCU.
Key points for selecting a socket for a burn-in MCU Points
For burn-in MCU sockets, it is necessary to select the optimum specifications depending on the usage method, usage environment, and important functions. Here, we will introduce the important points in determining the specifications of the socket for burn-in MCUs.
Point#1
Select either open top or clamshell from the method of setting the device
Point#2
If long life and contact stability are important, select contact pin plating.
In the case of mass-produced burn-in, long-term and repeated use is expected, so it is essential to extend the service life. If the device’s PKG lead plating is Sn-based, select ES-plated contact pins.
Point#3
If you need high heat dissipation, select the heat dissipation pin
If you are concerned about thermal runaway due to the heat generated by the PKG during the burn-in test, and if your device has a heat dissipation PAD, be sure to select the heat dissipation pin in conjunction with the heat dissipation simulation.
Sockets for burn-in MCUs Common problems Issues
Issue #1
Thermal runaway due to PKG's self-heating
Devices with high self-heating of PKG may cause thermal runaway during burn-in tests in high temperature environments. If this happens, you will not be able to perform a burn-in test.
Solutions
Heat dissipation simulation by thermal analysis + Heat dissipation with heat dissipation pin!
Issue #2
The ball and pin do not make good contact
Sockets and devices are elaborately crafted, but if the PKG warps during the burn-in test, the position of the ball may change and pinching with contact pins may not work, resulting in poor contact. If good contact is not possible, the burn-in test will not work, so it is necessary to devise ways to ensure stable contact even if the PKG warps.
Solutions
Two-point contact method Improves contact reliability with contact pins
Issue #3
Yield drops due to repeated BI
When using standard Au-plated contact pins, the tin plating of PKG leads is transferred and peeled off to the contact pins due to repeated BI processes, exposing the base of the contact pins, resulting in loss of contact.
Solutions
Increased contact pin life and yield by ES plating
Socket for burn-in MCU
Supported Packages
Our socket solution for burn-in MCUs Solutions
IC Socket Solutions.com offers IC socket solutions that apply a wealth of experience and simulation technology to all the challenges that arise when burn-in testing an MCU.
-
QFP/SOP Open Top Socket with Ground Pins
Stable Contact Performance with Cantilever Structure (2-Point Contact)
Ground Pins for Continuity Testing and Heat Dissipation Pins for High-Heat Packages -
Non-magnetic Socket
Non-magnetic socket will be required for sensor application
Corrosion resistance with non-magnetic performance -
Open top BGA two contact socket
Stable contact performance due to (two-point contact) structure
Double door structure makes it easy to insert PKG -
Open Top QFP/SOP pinch type socket
Pinch type contact (2-point contact) makes stable contact
Contact pin surface cleaning function prevents from accumulating debris due to the step between the bottom pin and the molded body surface. -
LCF series (general-purpose molded frame)
Low price and quick delivery for various devices up to 100mmx100mm
Replacible on site by surface mounting method -
Socket with heat sink
Heat Sink will reduce the increase of device temperature by contacting device surface with this parts and radiating the device heat into the air.
-
Super Shrink Socket
Increase of BIB density (1.8 times better density rate per 1 BIB)
In the condition of same socket qty, the reduction of BIB qty (45% reduction) -
ES Plating
By developing special plating (ES plating), the life of burn-in socket contacts has been extended in high temperature environments.
Maintenance costs have also been significantly reduced by reducing re-gold plating costs, etc. -
AM contact series
Low price and quick delivery for various devices by using machined Contact unit
Replacible on site by surface mounting method
Please feel free to contact us with
your questions regarding burn-in sockets.
Contact Us
- Is it possible to manufacture a socket with more than 10,000 pins?
- Do you have any solutions for heat dissipation?
- Can you support burn-in at temperatures above 150℃?
- Can you make sockets for unique, custom-made packages?Since the socket will be used for System Level Testing, devices will be tested in high volume and it is important that the devices can be easily placed and removed.
- Do you have any solution for improving contact performance?
- Is it possible to support high pins counts of BGA socket?
- How do you prevent the BGA heating with the socket ?
- Can the BGA socket support ultra-fine pitch?
- What kind of analysis can you provide ?
- Is there export to overseas and get local support?
- What should I do if there is a problem?
- What is the guaranteed cycle?
- What temperature can it be used in?
- I would like to consider a burn-in socket, but what information do you need?
- How long does it take to deliver?
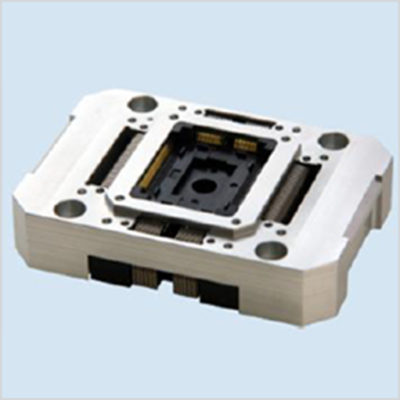
IC Socket Solution.com’s sockets for test MCUs contact the lead terminals with contacts for electrical connection, and employ probe pins and press pins as contacts. Assuming that the PKG is pressed by the handler, this model has an open top surface of the socket, and it is possible to manufacture a cover for pressing the PKG for manual use. In addition, for models that use a surface pressure welding method that is easy to maintain, and for sockets that use press pins, the combination of a resin molded housing and a machined socket frame has realized cost reduction.
Since the contact holder holding part (unit, resin molded housing) is removable, it is possible to replace all contact pins by replacing the holding part, or to replace only one specific pin.
Key points for selecting a socket for a test MCU Points
For the socket for the test MCU, it is necessary to select the optimum specifications according to the usage method, usage environment, and important functions. Here, we will introduce the important points in determining the specifications of the socket for the test MCU.
Point#1
Select with / without cover depending on how to use the test socket
If you want to use it in a mass production test site, it will be a model without a cover, but if you want to use it in manual evaluation, select a model with a cover. The cover can be removed.
Point#2
Select a dedicated contact method for micro signal evaluation
Devices that handle minute signals, such as MCUs, cannot accurately pick up signals using the contact pins used in ordinary test sockets. In that case, use a Kelvin contact dedicated to minute signals.
Sockets for test MCUs Common problems Issues
Issue #1
Cannot reliably evaluate micro signal characteristics
In the electrical characteristics test of the MCU, it is necessary to confirm whether it works with a minute signal, but it is not possible to reliably evaluate the minute signal characteristics with a contact pin for a normal test socket.
Solutions
Uses Kelvin contact pins that can cancel the effect of contact pins on PKG characteristics
Issue #2
Frequent replacement due to wear and solder adhesion of contact pins
Since it is used repeatedly in mass production tests, if the contact pin is a standard beryllium copper plated with gold, wear and Sn adhesion will progress at the tip of the pin, and as a result, poor contact is likely to occur.
Solutions
The carbon coating prevents solder transfer, extending the life of contact pins.
Issue #3
I want to carry out mass production tests at high temperatures in a stable manner.
The standard type contact pins are gold-plated beryllium copper, but in a high-temperature test environment, solder adheres to the gold plating quickly, plating peeling / base exposure occurs, and contact failure is likely to occur.
Solutions
The carbon coating prevents solder transfer, extending the life of contact pins.
Socket for burn-in MCU
Supported Packages
Our socket solution for Test MCUs Solutions
IC Socket Solution.com provides IC socket solution that applies abundant achievements and simulation technology to all the problems that occur when conducting the final test of MCU.
-
Conductivity Carbon Coating
Achieved a significant longer life of contacts by preventing solder migration
Achieved high durability with high slidablity and hardness -
ES Plating
By developing special plating (ES plating), the life of burn-in socket contacts has been extended in high temperature environments.
Maintenance costs have also been significantly reduced by reducing re-gold plating costs, etc.
Kelvin Contact
Type | Pitch | Pin Number | Mold |
---|---|---|---|
Press Pin | 0.5 | 48 | 7x7 |
64 | 9.8x9.8 | ||
100 | 14x14 | ||
116 | 14x20 | ||
128 | 14x20 | ||
0.65 | 70 | 14x25 | |
92 | 14x20 | ||
100 | 14x20 | ||
Probe Pin | 0.5 | 128 | 14x20 |
Single Contact
Type | Pitch | Pin Number | Mold |
---|---|---|---|
Press Pin | 0.8 | 44 | 10x10 |
0.65 | 100 | 14x20 | |
0.65 | 100 | 14x14 | |
128 | 14x20 | ||
Probe Pin | 0.5 | 64 | 10x10 |
128 | 14x20 | ||
144 | 20x20 |
Please feel free to contact us with
your questions regarding test sockets.
Contact Us
- Is it possible to manufacture a socket with more than 10,000 pins?
- Do you have any solutions for heat dissipation?
- Can you support burn-in at temperatures above 150℃?
- Are there sockets for writing program data?
- Can you make sockets for unique, custom-made packages?Since the socket will be used for System Level Testing, devices will be tested in high volume and it is important that the devices can be easily placed and removed.
- Is it possible to support high pins counts of BGA socket?
- Is it possible to support high frequencies in the BGA test socket?
- Can the BGA socket support ultra-fine pitch?
- What kind of analysis can you provide ?
- Is there export to overseas and get local support?
- What should I do if there is a problem?
- What is the guaranteed cycle?
- What temperature can it be used in?
- I would like to consider Enplas’s test socket. What kind of information I need to provide ?
- How long does it take to deliver?