Auto loading machine → Open top
Manual operation → Clam Shell
Special Package
-
Burn-in Sockets
Reliability Assessment /
For Mass Production -
Test Sockets
Property Assessment /
For Mass Production
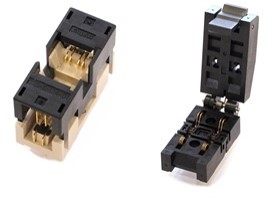
The burn-in socket for special PKG is an inexpensive socket made of molded method, considering in mind of package such as TO system.
In order to achieve high contact reliability, there is a two-point contact solution that sandwich the tip of package lead. There are also bottom contact pin options that enable to contact multiple pin for high current solutions. We can also provide that Heatsink option for heat dissipation purpose.
A unique / special shape package and multi pitch solutions, we are capable of making contact unit by machined process. This enable user to reduce the initial development cost.
Selecting points for BGA socket for burn-in Points
For burn-in sockets, it is important to select based on the usage and environment.
We introduce the key points to determine the specifications of the Special Package for burn-in usage.
Point#1
Select either open top or clamshell based on method of setting the device.
Point#2
Select the mounting method on the board by either focusing on contact reliability or focusing on maintainability.
Select the solder mounting method if you want to emphasize the contact reliability between the socket and the board, and select the surface mount method if you want to emphasize maintainability.
Solder mounting method / Emphasis on contact reliability
Using 2 points pinch type pin with above 0.65mm pitch. BGA sockets are relatively inexpensive because they are mainly made with molded method.
Surface mount method / Emphasis on maintainability
Using bottom contact probe with vertical movement and more effective for Package warpage. Machined pin options available that enable to support the fine / multi pitch.
Point#3
Consider the method for heat dissipation and high current solutions.
We provide the most applicable heatsink style after running heat simulation. For high current solution, we are able to suggest bypass pin options as necessary.
Special Package t for burn-in Common problems Issues
Since the special package socket for burn-in require to have stable performance even in a harsh environment, it is necessary to incorporate measures to avoid troubles in advance by utilizing simulation technology. Here are some common problems you may have when using BGA sockets for burn-in and solutions to them.
Issues #1
Thermal runaway due to PKG's self-heating
Devices with high self-heating of PKG may cause thermal runaway during burn-in tests in high temperature environments. If this happens, you will not be able to perform a burn-in test.
Solutions
Utilize thermal analysis simulation and avoid it by installing the optimum heat sink.
Issues #2
Pin melts with high current
When contact is unstable between package and socket, there is risk that high current flows one point which could potentially cause the pin melting.
Solutions
Run the Contact simulation with actual PKG size measurement.
Issues #3
Repeated burn-in testing reduces yield
For Au-plated contact pins, the base material of the contact pin may be exposed as the burn-in process is repeated. If this happens, the tin plating on the PKG Pad will be peeled off and transferred, and the contact between the socket (contact pin) and the device will become poor. As a result, the burn-in test will be NG and the yield with the device will decrease.
Solutions
Achieves a long life with contact pins that use ES plating.
Special Package
Burn In socket lineup for Speacial Package Solutions
IC Socket Solutions.com offers socket solutions that apply a bulit experience and simulation technology to all the challenges that arise when burn-in testing special PKG devices.
-
Non-magnetic Socket
Non-magnetic socket will be required for sensor application
Corrosion resistance with non-magnetic performance -
Sockets for power devices
Compatible with various power devices that are not handled by other companies
It is also possible to consider the optimum pin arrangement and support large currents of power devices. -
Socket with heat sink
Heat Sink will reduce the increase of device temperature by contacting device surface with this parts and radiating the device heat into the air.
-
Individual Temparature Control System
Heater and temperature sensors can be attached to control the temperature of the device for each socket.
Achieves more accurate temperature control in comparison with general burn-in equipment (temperature setting ± 3 ° C) -
ES Plating
By developing special plating (ES plating), the life of burn-in socket contacts has been extended in high temperature environments.
Maintenance costs have also been significantly reduced by reducing re-gold plating costs, etc. -
AM contact series
Low price and quick delivery for various devices by using machined Contact unit
Replacible on site by surface mounting method
Burn In socket lineup for Speacial Package Lineup
Supported PKG record | ||||
---|---|---|---|---|
MAX247 | H2PAK | HIP247-LL | D2PAK | I2PAK |
TO-247 long lead | TO-247-3L | TO-247-4L | TO-262-3L |
Please feel free to contact us with
your questions regarding burn-in sockets.
Contact Us
- Can you make sockets for unique, custom-made packages?Since the socket will be used for System Level Testing, devices will be tested in high volume and it is important that the devices can be easily placed and removed.
- What kind of analysis can you provide ?
- Is there export to overseas and get local support?
- What should I do if there is a problem?
- What is the guaranteed cycle?
- What temperature can it be used in?
- I would like to consider a burn-in socket, but what information do you need?
- How long does it take to deliver?
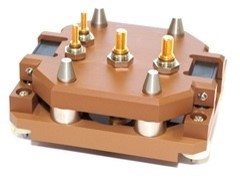
Since the contact pin holding part (unit) of the special PKG test socket is removable, it is possible to replace all contact pins by replacing the unit, or to replace only one specific pin. In addition, the unit uses FR4 material, which has a cost advantage, and the target PKG size (pitch, number of pins, pin arrangement, etc.) can be changed by replacing the unit.
Points for selecting Special Package for test POINTS
Test socket
For test sockets for speacial PKG, it is important to select based on the usage and environment.
We introduce the key points to determine the specifications of the Speceial PKG for Test Socket usage.
Point1
Select the most suitable probe pin according to the requirements of electrical characteristics
The leads through which a large current flows are contacted with multiple contact pins to ensure the withstand current characteristics.
Point2
If contact stability is important, adjust the pin tip shape and stroke amount.
Since the crown shape at the tip of the pin has more protrusions, it is more advantageous for contact, so we will adopt a 4-point crown specification that has a cost advantage, and 6-point and 8-point crowns if more importance is placed on contact. Also, we select a pin that can adjust the stroke amount according to the device.
Point3
Consider methods for heat dissipation and large current depending on the characteristics of PKG.
In order to prevent thermal runaway due to heat generation of PKG, consider a heat sink after performing heat generation simulation. Also, if it is compatible with large currents, consider contacting with multiple contact pins.
Special Package for Test socket Common problems Issues
Since the special pkage socket for test socket require to have stable performance even in a harsh environment, it is necessary to incorporate measures to avoid troubles in advance by utilizing simulation technology. Here are some common problems you may have when using special PKG for test and solutions to them.
Issues #1
Pin melts with high current
If the withstand current of the contact pin is not sufficient, or if the current flow is biased due to contact problems, the heat from the high current will melt the pin.
Solutions
Withstand current is secured by contacting multiple contact pins on the same PAD!
Issues #2
Thermal runaway due to PKG's self-heating
Since the special PKG often carries a large current, there is a risk of thermal runaway due to self-heating. It is necessary to take measures to enable efficient heat dissipation.
Solutions
Utilize thermal analysis simulation and avoid it by installing the optimum heat sink!
Furthermore, the device is cooled by combining a heat sink and a fan!
Special Package
Our Speacial Package solution for Test Solutions
-
Chip Contactor
Huge cost reduction of chip contactor which supports high current with tooled contact pin and contact module
Moduled contact pin related component makes it easier to exchange the parts on site. -
Conductivity Carbon Coating
Achieved a significant longer life of contacts by preventing solder migration
Achieved high durability with high slidablity and hardness -
ES Plating
By developing special plating (ES plating), the life of burn-in socket contacts has been extended in high temperature environments.
Maintenance costs have also been significantly reduced by reducing re-gold plating costs, etc.
Our Speacial Package line up for Test Lineup
Supported PKG record | ||||
---|---|---|---|---|
MAX247 | H2PAK | HIP247-LL | D2PAK | I2PAK |
TO-247 long lead | TO-247-3L | TO-247-4L | TO-262-3L |
Please feel free to contact us with
your questions regarding test sockets.
Contact Us
- Can you make sockets for unique, custom-made packages?Since the socket will be used for System Level Testing, devices will be tested in high volume and it is important that the devices can be easily placed and removed.
- What kind of analysis can you provide ?
- Is there export to overseas and get local support?
- What should I do if there is a problem?
- What is the guaranteed cycle?
- What temperature can it be used in?
- I would like to consider Enplas’s test socket. What kind of information I need to provide ?
- How long does it take to deliver?