Select the open top type when moving the device in and out by machine, and the clamshell type when inserting and removing it by hand.
SOP socket
-
Burn-in Sockets
Reliability Assessment /
For Mass Production -
Test Sockets
Property Assessment /
For Mass Production
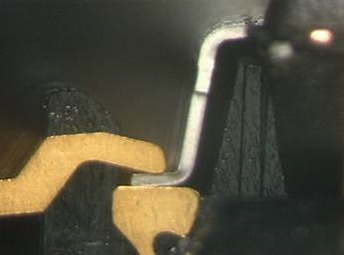
The burn-in SOP socket connects the contact pin with the SOP terminal to pass an electrical connection. There are two types of contacts: one is that a stamping pin sandwiches the lead, and another one is that probe pin pierces the lead. For the open top socket, we provide a design that enhances the pin contactability by the sandwiching structure (two-point contact), which can also reduces solder debris such as prevention of impurity accumulation due to the step between the bottom pin and the molded surface
Enplas Semiconductor Peripheral Corporation, which operates IC Socket Solution.com, also provides heat dissipation solutions for heat-generating PKG.
Points for selecting SOP sockets for burn-in Points
For burn-in SOP sockets, it is necessary to select the appropriate socket specifications depending on the test method, environment, and important functions. Here, we introduce the important points in determining the specifications of the SOP socket for burn-in.
Point#1
Select either open top or clamshell from the method of setting the device
Point#2
Decide how to position (guide) the package
Select the mold guide method when you place importance on firm positioning and stability, such as in mass production, and the lead guide method when you want to have versatility so that you can handle changes in PKG thickness.
Point#3
Consider methods for heat dissipation and large current depending on the characteristics of PKG
As a measure to prevent thermal runaway due to heat generation of PKG, consider a heat sink after performing heat generation simulation. If it is compatible with large currents, consider using a bypass pin.
Burn-in SOP socket common problems Issues
Since the SOP socket for burn-in needs to exhibit stable performance even in a harsh environment, it is necessary to incorporate measures to avoid troubles in advance by utilizing simulation technology. Here are some common problems you may have when using burn-in SOP sockets and solutions to them.
Issues #1
Thermal runaway due to PKG's self-heating
Devices with high self-heating may cause thermal runaway during burn-in tests in high temperature environments. If this happens, burn-in test cannot be completed.
Solutions
Utilize thermal analysis simulation and avoid it by installing the appropriate heat sink!
Issues #2
Repeated burn-in tests scratch PKG
Repeated burn-in tests inevitably generate solder debris, which can lead to cosmetic problem. In addition, PKG may be caught by the generated debris.
Solutions
Solve it with our unique wiping technology, already used by many customer.
Issues #3
Repeated burn-in reduces device yield
For Au-plated contact pins, the base of the contact pin may be exposed as the burn-in process is repeated. If this happens, the tin plating on the PKG lead will be transferred and peeled off, and the contact between the socket (contact pin) and the device will be poor. As a result, the burn-in test will be failed or the yield with the device will decrease.
Solutions
ES plating will bring a longer lifespan.
SOP socket
Solutions
-
High-Frequency Socket for System-Level Testing
Enhanced Grounding and Excellent High-Frequency Characteristics Achieved by Plating the Housing
Supports PAM4 Serdes 112Gbps Operation -
High Pin Count Solutions
Achieves stable contact performance and long life.
High current capacity is possible with integrated springs. -
QFP/SOP Open Top Socket with Ground Pins
Stable Contact Performance with Cantilever Structure (2-Point Contact)
Ground Pins for Continuity Testing and Heat Dissipation Pins for High-Heat Packages -
Non-magnetic Socket
Non-magnetic socket will be required for sensor application
Corrosion resistance with non-magnetic performance -
Sockets for power devices
Compatible with various power devices that are not handled by other companies
It is also possible to consider the optimum pin arrangement and support large currents of power devices. -
Socket with heat sink
Heat Sink will reduce the increase of device temperature by contacting device surface with this parts and radiating the device heat into the air.
-
ES Plating
By developing special plating (ES plating), the life of burn-in socket contacts has been extended in high temperature environments.
Maintenance costs have also been significantly reduced by reducing re-gold plating costs, etc. -
AM contact series
Low price and quick delivery for various devices by using machined Contact unit
Replacible on site by surface mounting method
SOP sokcet lineup for Burn In Lineup
Socket | Pitch | 16pin | 24pin | 32pin | 44pin | 48pin | 52pin | 64pin | 68pin | 70pin | 80pin | 92pin | 100pin | 112pin | 116pin | 118pin | 120pin | 128pin | 132pin | 144pin | 164pin | 172pin | 176pin | 196pin | 208pin | 216pin | 256pin |
---|---|---|---|---|---|---|---|---|---|---|---|---|---|---|---|---|---|---|---|---|---|---|---|---|---|---|---|
Open Top | 0.4mm | #bg# | |||||||||||||||||||||||||
0.5mm | #bg# | ||||||||||||||||||||||||||
0.635mm | #bg# | ||||||||||||||||||||||||||
0.65mm | #bg# | ||||||||||||||||||||||||||
0.8mm | #bg# | ||||||||||||||||||||||||||
1.0mm | #bg# | ||||||||||||||||||||||||||
Clam Shell | 0.4mm | #bg# | |||||||||||||||||||||||||
0.5mm | #bg# | ||||||||||||||||||||||||||
0.635mm | #bg# | ||||||||||||||||||||||||||
0.65mm | #bg# | ||||||||||||||||||||||||||
0.8mm | #bg# | ||||||||||||||||||||||||||
1.0mm | #bg# | ||||||||||||||||||||||||||
1.27mm | #bg# |
Please feel free to contact us with
your questions regarding burn-in sockets.
Contact Us
- Is it possible to manufacture a socket with more than 10,000 pins?
- Can you make sockets for unique, custom-made packages?Since the socket will be used for System Level Testing, devices will be tested in high volume and it is important that the devices can be easily placed and removed.
- What kind of analysis can you provide ?
- Is there export to overseas and get local support?
- What should I do if there is a problem?
- What is the guaranteed cycle?
- What temperature can it be used in?
- I would like to consider a burn-in socket, but what information do you need?
- How long does it take to deliver?
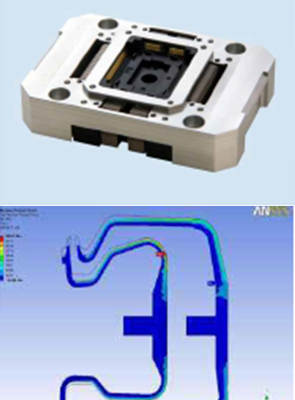
Among the test sockets, the test SOP socket is required to have a particularly long life and high current capacity. When importance is placed on electrical characteristics, the short-length probe pin supports high current in the Kelvin test, and the hard Pd alloy also supports the long life of the contact. If you are looking for a stable contact and long life, press-type pin with surface pressure contact can be selected. Since the press-type Kelvin contact socket is a surface pressure welding method, it is easy to replace the pin when it is worn out, suitable solution for mass production test applications.
Enplas Semiconductor Peripheral Corporation, which operates IC Socket Solution.com, solves all the problems of SOP sockets for final testing.
Points for selecting SOP sockets for test POINTS
For test SOP sockets, it is necessary to select the appropriate socket specifications depending on the test method, environment, and important functions. Here, we introduce the important points in determining the specifications of the SOP socket for test.
Point1
Select the suitable pin according to the required specifications and requirements
Select a contact pin according to test specifications and requirements, such as probe pins when electrical characteristics are important, press pins when high current and high temperature are required, and press pins are always price-competitive.
Point2
If contact stability is important, adjust the pin tip shape and stroke amount
Since the crown shape at the tip of the pin has more protrusions, the more the protrusions are, the more advantageous the contact is. Also, select a pin that can adjust the stroke amount according to the device.
Point3
Select the material of the contact pin tip according to the required durability
In order to improve wear resistance, carbon coating is applied to the tip of the contact pin, or the material of the tip of the pin is changed to Pd alloy or SK material to improve durability against wear or prevent Sn from adhering to the contact pin. It leads to the improvement of life and contact stability.
Test SOP socket common problems Issues
Since the test SOP socket needs to show stable performance even in a harsh usage environment, it is necessary to incorporate measures to avoid troubles in advance by utilizing simulation technology. Here are some common problems you may have when using test SOP sockets and solutions to them.
Issues #1
I want to improve the durability of the socket
Durability is important because the test SOP socket is used repeatedly in many cases. The standard contact pin is made of BeCo plated with Au, but if the pin tip is used repeatedly, wear and Sn adhesion will progress, and as a result, poor contact will easily occur.
Solutions
Avoid pin wear by using Pd plating and SK material.
The carbon coating avoids deterioration of contact due to Sn plating adhesion.
Issues #2
I cannot reliably evaluate micro signal characteristics
In the electrical characteristic test, it is necessary to confirm whether it works with a minute signal in particular, but it is not possible to reliably evaluate the minute signal characteristic because the increase in resistance value cannot be suppressed with a contact pin for a normal test socket.
Solutions
Use Kelvin contact pin (probe pin option and press pin option) to minimize the signal noise.
Issues #3
PKG dimensional variation is large and contact is not stable
If the SOP package has a large variation in dimensions, positioning will become unstable and poor contact will occur easily. These package dimensional variations need to be absorbed by increasing the contact margin in the test SOP socket.
Solutions
Increase the margin with multi-point contact solution and solve contact failure!
Issues #4
I want a test socket that can handle large current
In the case of SOP packages, there are many cases where high current support is required, such as when 10 Amp or more are applied per pin, but normal contact pins do not support this. Therefore, it is necessary to select a contact pin that supports high current.
Solutions
Press-type Kelvin contact socket for high current achieves stable contact and long life.
SOP socket
Solutions
-
High-Frequency Socket for System-Level Testing
Enhanced Grounding and Excellent High-Frequency Characteristics Achieved by Plating the Housing
Supports PAM4 Serdes 112Gbps Operation -
High Pin Count Solutions
Achieves stable contact performance and long life.
High current capacity is possible with integrated springs. -
Spring Kelvin Contact
Achieves stable contact performance and long life.
High current capacity is possible with integrated springs. -
Conductivity Carbon Coating
Achieved a significant longer life of contacts by preventing solder migration
Achieved high durability with high slidablity and hardness -
ES Plating
By developing special plating (ES plating), the life of burn-in socket contacts has been extended in high temperature environments.
Maintenance costs have also been significantly reduced by reducing re-gold plating costs, etc.
SOP sokcet lineup for Test Lineup
Pitch | Operation Temperature | Lifetime | Load | Contact Resistance | Current | |
---|---|---|---|---|---|---|
Press Kelvin | 0.4mm | -65℃~150℃ | 500,000 times | 45gf | 100mΩ | 8A |
0.5mm | ||||||
0.65mm | ||||||
0.8mm | ||||||
1.0mm | ||||||
1.27mm |
pitch | Operation Temperature | Lifetime | Load | Insertion Loss/ Reflection Loss | |
---|---|---|---|---|---|
Capsule Pin | 0.5mm | -55℃ ~ +125℃ | 200,000 times | 25gf | >20GHz at -1dB / >20GHz at -10dB |
0.8mm | 250,000 times | ||||
Probe Pin | 0.8mm | 200,000 times | |||
0.5mm | 200,000 times | ||||
0.4mm | 1,000,000 times |
Please feel free to contact us with
your questions regarding test sockets.
Contact Us
- Is it possible to manufacture a socket with more than 10,000 pins?
- Can you make sockets for unique, custom-made packages?Since the socket will be used for System Level Testing, devices will be tested in high volume and it is important that the devices can be easily placed and removed.
- What kind of analysis can you provide ?
- Is there export to overseas and get local support?
- What should I do if there is a problem?
- What is the guaranteed cycle?
- What temperature can it be used in?
- I would like to consider Enplas’s test socket. What kind of information I need to provide ?
- How long does it take to deliver?