The most crucial aspect of burn-in sockets is their ability to perform reliable screening and to measure consistently even after hours of repeated use at high temperatures. In particular, they must have high and stable contact properties in their contact pins.
Burn-in sockets
What is a burn-in test?
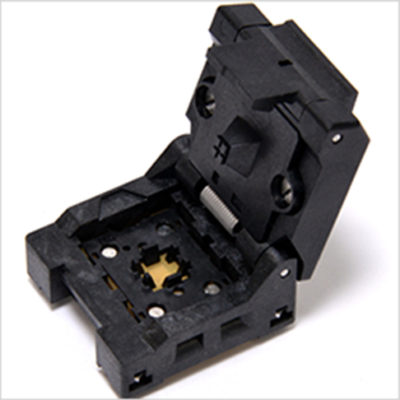
The burn-in test is an accelerated test used to identify initial defects in semiconductors and devices. Typically, this stress test involves powering the semiconductor for several hours in a 125°C environment. By intentionally inducing initial defects in this way, the failure rate in the market is reduced, as defective products are eliminated before shipping. Burn-in tests are commonly conducted on automotive products that require particularly high reliability among semiconductor devices. However, to improve the yield rate even for devices with poor manufacturing yields, such as memory and high-power systems, a burn-in test is also performed. There are two types of burn-in tests: (1) mass production burn-in and (2) reliability evaluation.
As various devices, including automobiles, become more digitalized, the need to enhance the reliability of semiconductors and devices and minimize the release of defective products into the market grows increasingly crucial. Thus, the role of the burn-in test is becoming more important.
What is a burn-in test?
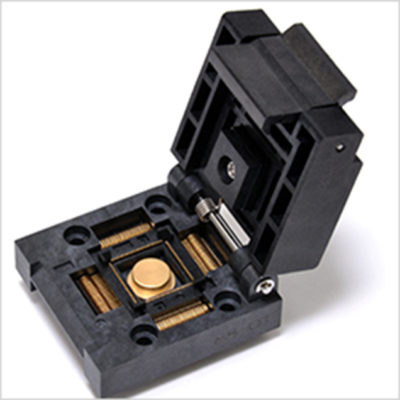
Burn-in sockets are package-specific sockets used to conduct burn-in testing of semiconductors and devices in high-temperature environments. Although burn-in tests are usually performed at 125°C, devices used in automotive applications such as “running,” “turning,” and “stopping”—particularly those around the engine—are tested at even higher temperatures. Burn-in sockets are required to operate stably under these harsh conditions, and high performance is essential. In response to this trend, the recent development of semiconductors and devices is accelerating towards a wide variety of products in small quantities, increasing the demand for burn-in sockets.
Applications that require burn-in testing
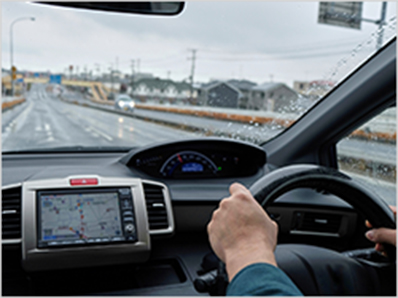
Auto Motive
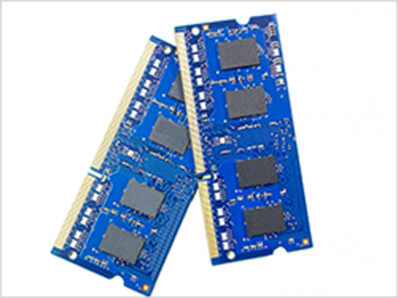
Memory
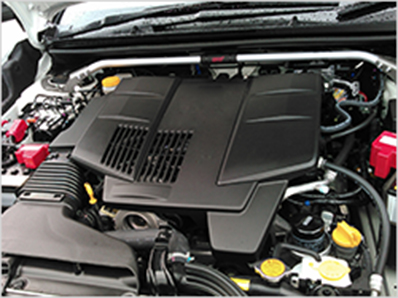
High power
Recent Burn-in Test Trends
As the digitization of everyday devices continues to expand, the number and types of semiconductors and devices will only grow. With this trend, electronic devices are increasingly required to have higher reliability and lower defect rates. Among these, in-vehicle systems like ADAS (Advanced Driver Assistance Systems) and CASE (connected, autonomous driving, sharing, and electrification) are experiencing rapid growth. In these areas, measures to drastically reduce the defect rate are essential. To meet the demands and challenges of this market, burn-in sockets must also be designed to withstand higher temperatures, and to be more reliable and reproducible.
What is required of burn-in sockets
As the market changes and the needs for burn-in testing increase, there are three major requirements for burn-in sockets.
Being able to perform reliable screening
Being able to test under certain conditions even in a high temperature environment
High workability
Mass-produced or high-volume devices often require repeated insertion and removal using a single burn-in socket. Consequently, the burn-in test must be compatible with automated equipment. In addition to automated equipment, manual sockets can also be used for tasks such as reliability evaluations involving smaller quantities, but high workability remains crucial.
Are you encountering issues with burn-in sockets? Are you encountering any issues?
Enplas Semiconductor Peripheral Corporation, operated by Enplas, is a leading manufacturer providing burn-in sockets as a solution for a variety of issues. Burn-in socket lineups are available for a variety of applications, devices and packages, so be sure to search according to your applicable category.
- Choose by device
- Choose by PKG
Burn-in Socket Solutions Solutions
Semiconductors and devices are evolving, and there is growing need to support more demanding conditions. As a result, burn-in sockets are required to address more and more issues every day. Enplas Semiconductor Peripheral Corporation, operated by Enplas, offers the below solutions to address various issues relating to burn-in sockets.
-
High-Frequency Socket for System-Level Testing
Enhanced Grounding and Excellent High-Frequency Characteristics Achieved by Plating the Housing
Supports PAM4 Serdes 112Gbps Operation -
High Pin Count Solutions
Achieves stable contact performance and long life.
High current capacity is possible with integrated springs. -
QFP/SOP Open Top Socket with Ground Pins
Stable Contact Performance with Cantilever Structure (2-Point Contact)
Ground Pins for Continuity Testing and Heat Dissipation Pins for High-Heat Packages -
Spring Probe Pin
Enplas's own design will provide internal short circuit of probe pin with low resistance value (Ave 50m ohm or under)
Enplas provides suitable socket design proposal to meet required specification -
Non-magnetic Socket
Non-magnetic socket will be required for sensor application
Corrosion resistance with non-magnetic performance -
Open top BGA two contact socket
Stable contact performance due to (two-point contact) structure
Double door structure makes it easy to insert PKG -
Open Top QFP/SOP pinch type socket
Pinch type contact (2-point contact) makes stable contact
Contact pin surface cleaning function prevents from accumulating debris due to the step between the bottom pin and the molded body surface. -
Custom socket for high power liquid cooling system
Not only BGA, and LGA, but also various type of package including QFN can be designed by using a socket that is suitable for the thermal head size
-
LCF series (general-purpose molded frame)
Low price and quick delivery for various devices up to 100mmx100mm
Replacible on site by surface mounting method -
Carrier Socekt
Easy package handling with carrier PCB
Multi-height pusher for different thickness devices -
Sockets for power devices
Compatible with various power devices that are not handled by other companies
It is also possible to consider the optimum pin arrangement and support large currents of power devices. -
Open Top Socket with Cover
Open top socket integrated with a mechanism that protects the entire top surface of the PKG.
Socket with cover to prevent dust in the air from coming into the socket. -
Improved cover handling socket for large devices
Enable to operate with stable pressing force for high pin count solutions.
-
Height adjustable socket
By just switching a lever, the height of Heat sink pressing surface is adjusted to enable one IC socket to test PKGs of different thickness.
-
Socket with heat sink
Heat Sink will reduce the increase of device temperature by contacting device surface with this parts and radiating the device heat into the air.
-
Burn-in socket with heat pipe
High heat dissipation performance due to the heat circulation structure of the heat pipe improves the accuracy of individual temperature adjustment tests for high heat generation PKG.
-
Individual Temparature Control System
Heater and temperature sensors can be attached to control the temperature of the device for each socket.
Achieves more accurate temperature control in comparison with general burn-in equipment (temperature setting ± 3 ° C) -
High pin count BGA socket (VC contact)
Stamped contact pin and molded frame realize significant cost reduction for large PKG
Replacible on site by surface mounting method -
Super Shrink Socket
Increase of BIB density (1.8 times better density rate per 1 BIB)
In the condition of same socket qty, the reduction of BIB qty (45% reduction) -
ES Plating
By developing special plating (ES plating), the life of burn-in socket contacts has been extended in high temperature environments.
Maintenance costs have also been significantly reduced by reducing re-gold plating costs, etc. -
AM contact series
Low price and quick delivery for various devices by using machined Contact unit
Replacible on site by surface mounting method
Please feel free to contact us with
your questions regarding burn-in sockets.
Contact Us
Please contact us if you have any questions relating to burn-in sockets. We have also compiled previous questions about IC socket solutions below, so please take a look.
- Is it possible to manufacture a socket with more than 10,000 pins?
- Do you have any solutions for heat dissipation?
- Can you support burn-in at temperatures above 150℃?
- Can you make sockets for unique, custom-made packages?Since the socket will be used for System Level Testing, devices will be tested in high volume and it is important that the devices can be easily placed and removed.
- I am considering an electrical inspection methods for LGA ceramic packaging (20 to 50 mm) with several thousand pins. Do you have a suitable socket for this device?